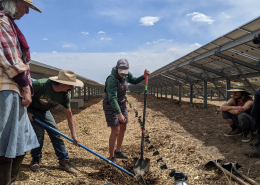
Case Study: Boulder Housing Partners Triangle Solar Array
The Boulder Housing Partners Triangle Solar Array is one of the first solar arrays in the Boulder, Colorado, area that is solely dedicated to offsetting energy use for low-income residents. The array is a south-facing fixed array with the leading edge of the solar panels about two feet off the ground. Construction was completed in 2021, and the array will generate over 19 GWh of solar energy in the next 10 years.
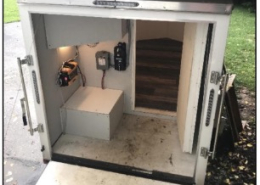
Reducing Post-Harvest Losses Through the Use of Innovative Solar-Powered Refrigeration Systems
Written for the AgriSolar Clearinghouse by Ridge to Reefs staff Emma Verlinden, Paul Sturm, and Phal Mantha
In 2017, the devastation following Hurricane Maria was catastrophic for countless coastal communities. The archipelago of Puerto…
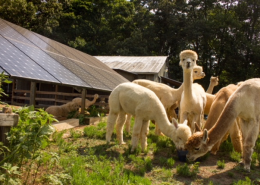
Case Study: Cozy Cove Farm
Just outside of Gurley, Alabama, a herd of grazing llamas and alpacas find refuge from the sun underneath a solar array. Tony and Cozette O’Neil, owners of Cozy Cove Farm, have been raising the animals since 1995, shearing their fleece to make yarn and felt. Today, the O’Neils are also proud renewable energy producers for their community, thanks to the 50-kW solar system that has been generating electricity since February 2013.
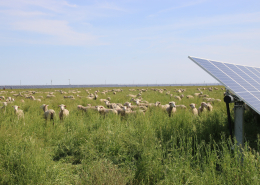
Case Study: Mustang Two Solar Facility
Indart sheep between rows of solar panels.
By Anna Richmond-Mueller, NCAT Energy Analyst
Just outside of Stratford, California, hundreds of sheep spend their days grazing between rows of solar panels at the Mustang Two solar park.…
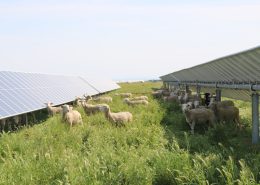
Case Study: Slate Solar PV Park
Indart sheep grazing around solar panels.
By Anna Richmond-Mueller, NCAT Energy Analyst
Located in Kings County, the Slate Solar PV Park produces power for hundreds of thousands of California citizens, while simultaneously providing…
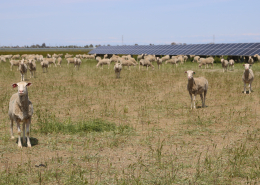
Case Study: Indart Solar Sheep Grazing
Indart sheep between rows of solar panels.
By Anna Richmond-Mueller, NCAT Energy Analyst
As the average age of the American farmer continues to rise, the question of how to transition an agricultural operation to the next generation…
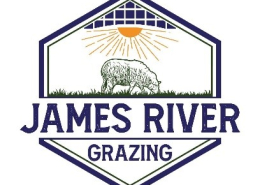
Case Study: James River Grazing
Sheep grazing at the Mechanicsville site.
By Anna Richmond-Mueller, NCAT Energy Analyst
Located near Richmond, Virginia, the Mechanicsville solar park is one of the state’s first utility-scale solar sites. Covering over 220 acres, the…
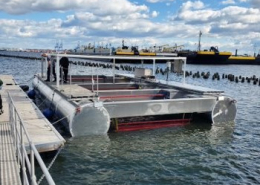
Case Study: Solar Oysters LLC
Solar panels powering the Solar Oyster Production System (SOPS) platform.
By Anna Richmond-Mueller, NCAT Energy Analyst
From filtering water to creating habitats for other marine species, oysters are a vital component of the Chesapeake…
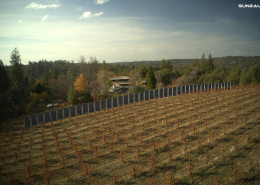
Case Study: Sunzaun Vertical Solar System
By Anna Richmond-Mueller, NCAT Energy Analyst
Sunstall, a California-based solar installer, is helping farmers harvest the sun twice with their new vertical solar system, known as Sunzaun. The Sunzaun vertical solar system was originally…
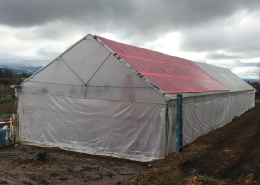
Case Study: Soliculture Research Greenhouse
By Anna Richmond-Mueller, NCAT Energy Analyst
When it comes to conversations surrounding energy and water use in the modern world, the agricultural industry’s consumption of both is often at the forefront. As the world’s population continues…